原标题:赋能直升机装配效率!哈飞自主研制AGV智能搬运车
来源:冰城+客户端
只需动动手指按下按钮,AGV就载着大型工装自动 “奔跑”到指定位置。哈飞人“顺手”自主研制出无人驾驶智能搬运设备近日投用,由此更高效推进直升机生产效率,缩短了哈产直升机装配周期。这个“跨界”,哈飞人干的漂亮。
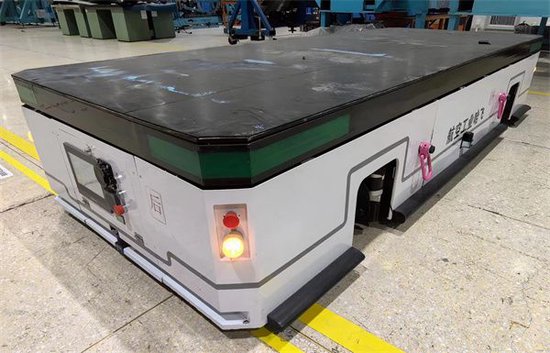
作为一种自动化无人驾驶的智能移动搬运设备,AGV是现代制造车间重要设备之一。近年来,随着哈飞高质量发展,相关生产车间内辅助直升机装配的运输设备出现了功能“瓶颈”。企业多年来使用的传统运输设备类似于小推车,装上模具、量具、零部件等工装后主要靠人拉、手推或专人在车间内驾驶实现运送。尽快使用AGV是哈飞的现实需要。
“直接采购AGV的成本高,返修要依赖厂家,周期长,费用也不少。”“我们应该研制出属于我们自己的AGV。”“这样在降低成本的同时,设计优化和返修都不是问题了……”在会议室,哈飞工程技术部和车间相关技术人员开展了一场关于降低AGV采购成本和保障直升机生产周期的研讨。
从无到有的创造很难,哈飞人说干就干。工程技术部牵头成立AGV降成本项目团队,并组建集结构设计、强度分析、电气自动控制、工业化设计于一体的AGV智能移动平台设计团队,向AGV自主研制迈出了第一步。随后,项目团队结合哈飞车间实际使用需求,先后与多家先进AGV制造厂家开展线上线下交流。综合考量使用车间地面环境、使用频率和工装成本等因素,项目团队确定选用舵轮移动控制系统和电动升降系统。
AGV需要满足型架的转运及对接,这对车体重量提出了要求。而车体过重又会使其与动力系统失调,影响动力系统精准度及使用寿命,这是团队遇到的第一个难题。为了实现轻量化设计,团队对车体结构进行分析,展开多方案优化设计。经多次验证和仿真分析,最终实现车体的最大承载与轻量化设计相兼容,难题迎刃而解。
随后,项目团队加紧研制步伐,对相关设计技术发起总攻,在一轮又一轮的方案评审优化中,实现了AGV自主设计的既定目标。日前,在工装制造车间和使用车间的通力协作下,长3.5米、宽1.5米、高0.65米的AGV完成制造装配及调试,顺利投用。
目前,这场长达一年半的AGV自主研制“拉力赛”已收官。在哈飞车间里,AGV正跑出哈飞降本增效的“加速度”,让哈产直升机更迅速飞向蓝天。